Cost to Replace Stucco with Vinyl Siding: A Comprehensive Guide
Considering replacing your stucco exterior with vinyl siding? The decision involves more than just aesthetics; it's a significant home improvement project with substantial financial implications. This guide delves into the intricacies of calculating the cost to replace stucco with vinyl siding, providing a detailed breakdown of expenses and offering insights to help you navigate this process effectively.
From understanding the initial cost comparison between stucco removal and vinyl siding installation to exploring material sourcing, labor costs, and permitting, we aim to equip you with the knowledge needed to make informed decisions. We’ll also address the impact of factors like house size, location, and weather on the overall project timeline and budget.
Cost Comparison
Replacing stucco with vinyl siding involves a significant investment. Understanding the cost breakdown for both materials is crucial for budgeting and planning your home improvement project. This section details the cost differences, influencing factors, and provides a comparative analysis to aid in your decision-making process.
Stucco Removal and Disposal Costs
The initial step in replacing stucco is its removal and proper disposal. This process is labor-intensive and can significantly impact the overall project cost. The average cost for stucco removal and disposal ranges from $2 to $5 per square foot, depending on the stucco's thickness, condition, and accessibility.
Factors such as the presence of lath (a supporting structure under the stucco) and the need for specialized equipment (like jackhammers) will also affect the cost. Disposal fees vary by location and the amount of waste generated. For a 2,000 square foot home, expect stucco removal and disposal costs to fall somewhere between $4,000 and $10,000.
This is a significant upfront expense that should be factored into the total project budget.
Material, Labor, and Permit Costs Comparison
The following table compares the material, labor, and permit costs for both stucco and vinyl siding installations. Costs are presented as ranges to reflect variations in quality and regional differences.
Cost Item | Stucco (Low-End) | Stucco (Mid-Range) | Stucco (High-End) |
---|---|---|---|
Material Cost per sq ft | $3
| $6
| $9
|
Labor Cost per sq ft | $5
| $8
| $11
|
Permit Fees | $200
| $500
| $1000
|
Cost Item | Vinyl Siding (Low-End) | Vinyl Siding (Mid-Range) | Vinyl Siding (High-End) |
---|---|---|---|
Material Cost per sq ft | $2
| $4
| $6
|
Labor Cost per sq ft | $3
| $5
| $7
|
Permit Fees | $200
| $500
| $1000
|
Note: Permit fees can vary significantly based on local regulations and the complexity of the project.
Factors Influencing Overall Cost
Several factors beyond material and labor costs can significantly impact the total expense of replacing stucco with vinyl siding.House size directly correlates with the overall cost. A larger house requires more materials and labor, resulting in a higher total cost.
For example, a 3,000 square foot house will cost significantly more than a 1,000 square foot house.Location plays a critical role. Labor costs and material prices vary regionally. Areas with a high cost of living tend to have higher labor rates and material prices.Accessibility of the house also influences cost.
Houses with difficult-to-reach areas, multiple stories, or complex architectural features may require more time and specialized equipment, thus increasing labor costs. For instance, a house with intricate detailing around windows or dormers will likely be more expensive to side than a simpler, more uniform structure.
Material Costs and Sourcing
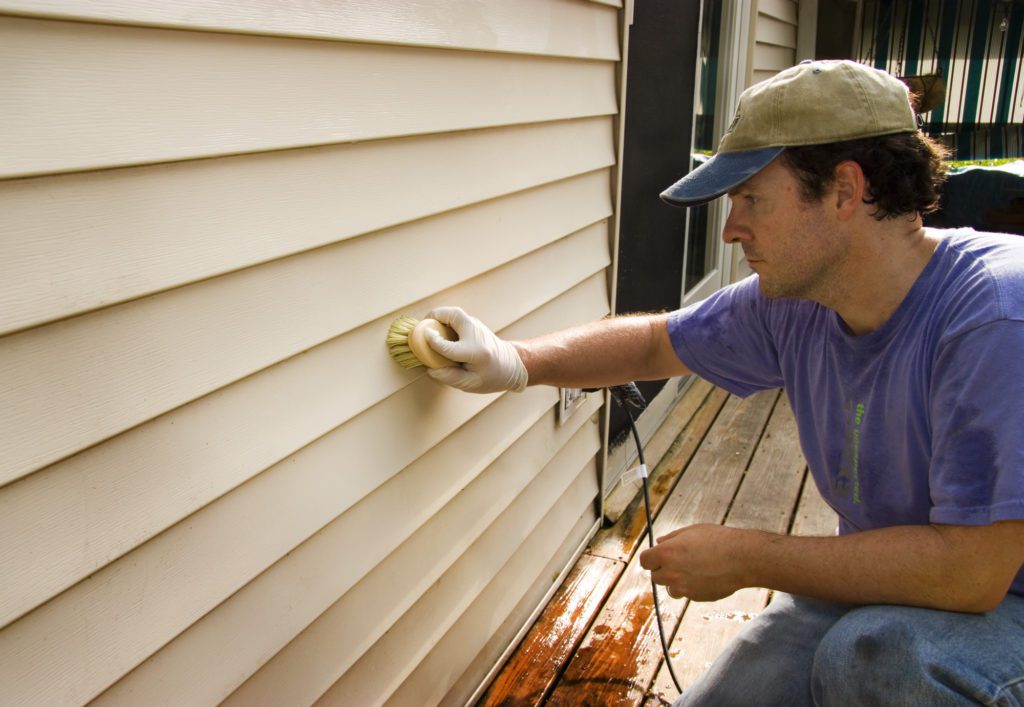
Choosing the right vinyl siding involves understanding the various material types and their associated costs. The initial investment in materials significantly impacts the overall project expense, and careful sourcing can lead to considerable savings. This section details the cost variations among different vinyl siding types, the process of finding reliable suppliers, and the long-term implications of material choice.
Vinyl Siding Types and Costs
Different vinyl siding types offer varying levels of durability, aesthetics, and, consequently, price. The price differences stem from the manufacturing process, material composition, and included features. Higher-end options often boast enhanced features like improved impact resistance, thicker profiles, and more realistic wood grain textures.
- Standard Vinyl Siding:This is the most economical option, typically ranging from $1 to $3 per square foot. It offers basic protection and a range of colors but may lack the durability and aesthetic appeal of higher-priced alternatives. The lifespan is generally 20-30 years with average maintenance.
- Premium Vinyl Siding:Premium vinyl siding, priced between $3 and $6 per square foot, incorporates enhanced features such as thicker gauge vinyl, improved UV resistance, and more realistic wood grain textures. It offers superior durability and a longer lifespan (30-40 years), often requiring less frequent maintenance.
- Insulated Vinyl Siding:This option combines vinyl siding with an insulating foam backing. While more expensive (ranging from $5 to $8 per square foot), it significantly improves energy efficiency, reducing heating and cooling costs over the siding's lifetime. The lifespan is comparable to premium vinyl siding, but maintenance costs may be slightly lower due to better protection against weather damage.
Sourcing Materials and Obtaining Quotes
Securing competitive pricing and ensuring material quality requires a systematic approach to sourcing. Begin by identifying reputable suppliers in your area. This might involve checking online reviews, asking for recommendations from contractors, and visiting local building supply stores.
It is crucial to compare quotes from multiple suppliers before making a decision.
When obtaining quotes, be sure to specify the exact type and quantity of vinyl siding needed, along with any necessary accessories like trim, flashing, and fasteners. Clarify the pricing structure – whether it includes delivery and any potential discounts for bulk purchases.
Confirm the supplier's return policy in case of damaged or defective materials. Reputable suppliers will readily provide detailed quotes, samples, and warranty information.
Lifespan and Maintenance Costs
The lifespan and maintenance requirements of vinyl siding vary considerably depending on the type and quality of the material. Higher-quality vinyl siding typically lasts longer and requires less maintenance than cheaper alternatives. Proper installation also plays a significant role in determining the longevity of the siding.
For instance, standard vinyl siding may require repainting or minor repairs after 20 years, while premium or insulated options might last 30-40 years with minimal maintenance beyond occasional cleaning. Regular cleaning with a pressure washer and prompt attention to any minor damage can extend the lifespan and reduce the need for costly repairs down the line.
Consider the total cost of ownership, including initial material costs, installation fees, and anticipated maintenance expenses over the siding's lifetime, when making your selection.
Labor Costs and Contractor Selection
Labor costs represent a significant portion of the overall expense when replacing stucco with vinyl siding. Understanding these costs and selecting a reliable contractor are crucial for a successful and cost-effective project. This section details the typical labor costs associated with each phase of the project and provides guidance on finding and vetting qualified contractors.
Hourly Rates for Skilled Laborers
The hourly rates for skilled laborers involved in stucco removal and vinyl siding installation vary depending on location, experience, and project complexity. However, a general range can be provided to offer a reasonable estimate. The following table illustrates these ranges:
Trade | Hourly Rate Range |
---|---|
Stucco Removal (Demolition Crew) | $40
|
Vinyl Siding Installer | $50
|
Framing/Repair Crew (if needed) | $55
|
Note: These are average ranges and may vary significantly based on geographic location and market conditions. Always obtain detailed quotes from contractors to get precise figures for your specific project.
Finding and Vetting Qualified Contractors
Finding a qualified contractor involves several steps to ensure a smooth and successful project. Thorough vetting is essential to avoid potential problems down the line.The process typically involves:
- Online Research:Use online resources like Angie's List, Yelp, and HomeAdvisor to find local contractors and read reviews from previous clients. Look for contractors with a consistent history of positive feedback.
- Checking Licenses and Insurance:Verify that the contractor holds the necessary licenses and insurance, including general liability and workers' compensation insurance. This protects you from potential financial liability in case of accidents or damages.
- Requesting References:Ask for references from previous clients and contact them to inquire about their experience with the contractor. Inquire about the contractor's professionalism, timeliness, and the quality of their work.
- In-Person Interviews:Schedule in-person meetings with potential contractors to discuss the project in detail. This allows you to assess their communication skills, professionalism, and understanding of your needs.
- Reviewing Contracts Carefully:Before signing any contract, carefully review all terms and conditions, including payment schedules, project timelines, and warranty information. Ensure that all aspects of the project are clearly defined
Obtaining Multiple Quotes
Obtaining multiple quotes from different contractors is crucial for ensuring you receive a competitive price and fair assessment of the project. Comparing quotes allows you to identify potential discrepancies in pricing and scope of work. It's advisable to obtain at least three quotes from reputable contractors before making a final decision.
This competitive bidding process will help you secure the best value for your investment.
Project Timeline and Scheduling
Successfully completing a stucco-to-vinyl siding replacement project hinges on meticulous planning and scheduling. Understanding the typical timeline, potential delays, and the impact of weather is crucial for managing expectations and budget. This section Artikels a sample project timeline and addresses potential complications.A typical stucco-to-vinyl siding replacement project involves several distinct phases, each with its own time requirements.
Careful consideration of each phase ensures a smooth and efficient process.
Sample Project Timeline
The following timeline provides a general estimate. Actual durations may vary based on project size, complexity, and weather conditions. This example assumes a medium-sized single-family home.
Phase | Estimated Duration | Description |
---|---|---|
Stucco Removal | 3-5 days | Careful removal of existing stucco, including disposal of debris. This phase requires meticulous work to avoid damaging underlying sheathing. |
Wall Preparation | 2-4 days | Inspection and repair of any underlying sheathing, installation of water-resistant barriers, and preparation of the walls for siding installation. This may include patching, sealing, and priming. |
Vinyl Siding Installation | 5-7 days | Installation of vinyl siding, including cutting, fitting, and securing panels. This includes installing trim, flashing, and other necessary components. |
Final Cleanup | 1 day | Removal of debris and restoration of the surrounding area. |
Potential Delays and Mitigation Strategies
Several factors can potentially delay a stucco-to-vinyl siding replacement project. Proactive planning can minimize disruptions.
- Unexpected structural issues:Discovering rotted wood or other structural damage during stucco removal can significantly extend the project timeline. Regular inspections and pre-project assessments can help identify and address these issues early.
- Material delays:Supply chain issues or unexpected delays in material delivery can halt progress. Ordering materials well in advance and having backup options can mitigate this risk.
- Labor shortages:Finding and retaining skilled labor can be challenging. Securing a reliable contractor with a proven track record and sufficient workforce is crucial. A well-defined contract with clear timelines and payment schedules helps ensure the project stays on track.
- Permitting delays:Delays in obtaining necessary permits can stall the project. Submitting permit applications early and following up regularly can minimize delays.
Weather Conditions and Project Timeline
Weather significantly impacts the project timeline and cost. Rain, extreme heat, or freezing temperatures can halt work, extending the overall duration. Unexpected weather events can also lead to material damage or increased labor costs.
Unfavorable weather conditions can easily add a week or more to the project timeline, and potentially increase the overall cost by 10-15% or more due to delays and potential material replacements.
For example, a project scheduled for spring might encounter unexpected rain delays, pushing the completion date into summer, and increasing labor costs due to overtime or scheduling conflicts. Conversely, extreme heat can impact worker productivity and necessitate more frequent breaks, leading to a longer completion time.
Planning for contingencies, such as weather-dependent scheduling adjustments and contingency budgets, is vital.
Permitting and Legal Considerations
Replacing stucco with vinyl siding, while seemingly straightforward, necessitates navigating a landscape of local building codes and permitting requirements. Failure to obtain the necessary permits and adhere to regulations can result in significant penalties, including project stoppages, fines, and even legal action.
Understanding these legal aspects is crucial for a smooth and compliant renovation.The process of obtaining the necessary permits typically involves submitting a detailed application to your local building department. This application usually requires comprehensive documentation outlining the project's scope, including detailed plans and specifications.
These plans should clearly depict the existing stucco structure, the proposed vinyl siding installation, and any associated modifications to the building's exterior.
Required Documentation for Permit Applications
The specific documents required can vary depending on your location, but common examples include:
- Completed permit application form.
- Detailed project plans and specifications, including material specifications and installation methods.
- Site plans showing the property boundaries and the location of the work.
- Proof of property ownership.
- Contractor's license and insurance information (if applicable).
It is advisable to contact your local building department early in the planning stages to inquire about the specific requirements and to ensure all necessary documentation is included. Incomplete or inaccurate applications will delay the permitting process.
Relevant Building Codes and Regulations
Building codes and regulations are designed to ensure public safety and structural integrity. These codes often address aspects such as:
- Fire safety:Regulations may specify the type of vinyl siding that can be used, its fire resistance rating, and the required spacing between the siding and any combustible materials.
- Wind resistance:Codes often dictate the fastening methods and the overall structural integrity of the siding system to withstand high winds.
- Water resistance:Regulations address proper flashing and sealing techniques to prevent water damage and moisture intrusion.
- Accessibility:Codes might address requirements for accessibility features if the project involves modifications to entrances or walkways.
These codes are often enforced through inspections at various stages of the project. Non-compliance can lead to delays and additional costs. It's essential to work with a contractor who is familiar with these codes.
Penalties for Non-Compliance
Failure to obtain necessary permits or to comply with building codes can result in a range of penalties. These can include:
- Stop-work orders:The project may be halted until the necessary permits are obtained or the violations are rectified.
- Fines:Significant fines can be imposed for each violation, varying depending on the severity and the jurisdiction.
- Legal action:In some cases, legal action may be taken, resulting in costly legal fees and potential court orders.
- Insurance issues:Lack of permits may invalidate insurance coverage in case of accidents or damages during or after the project.
Ignoring building codes and permit requirements is a significant risk that can jeopardize the entire project and potentially result in substantial financial losses.
Visual Representations
The transformation of a house from stucco to vinyl siding is a significant aesthetic change, impacting both the immediate appearance and the overall curb appeal. Understanding these visual differences is crucial for homeowners considering this renovation. This section will detail the before-and-after appearance, highlighting color, texture, and the overall aesthetic shift, as well as the contrasting installation processes.Before the renovation, imagine a house clad in stucco.
Perhaps it's a warm, sandy beige, showing signs of age – minor cracks spider-webbing across the surface, a slightly uneven texture, and a faded color due to years of sun exposure. The overall feel might be somewhat dated, depending on the stucco's finish.
A smooth finish could appear sleek but potentially monotonous, while a textured finish, although adding depth, might show more imperfections over time.
Before and After Appearance
The "before" image presents a house with stucco, possibly exhibiting variations in color due to sun exposure or previous repairs. The texture might range from a smooth, almost flat surface to a more coarse, textured finish, depending on the stucco type and application.
Color may be muted or vibrant, reflecting the homeowner's original choices. Cracks or discoloration might be visible, indicating the need for replacement. The "after" image showcases the same house, now clad in vinyl siding. The new siding could be a bolder color, offering a fresh, modern look, or it might maintain a similar palette but with a more consistent and even tone.
The texture would be uniformly smooth, eliminating the irregularities of the old stucco. The overall aesthetic is cleaner, more contemporary, and likely more visually appealing to a wider range of tastes. For instance, a house originally clad in a dull, light brown stucco might be transformed with crisp white vinyl siding, instantly enhancing its brightness and modern appeal.
Conversely, a house with a vibrant, but uneven, red stucco could be given a consistent, deep red vinyl siding, improving its overall appearance.
Installation Process Comparison
The installation processes for stucco and vinyl siding differ significantly. Stucco application is a labor-intensive process requiring skilled labor. It involves preparing the wall surface, applying a base coat, a scratch coat, and a final finish coat. Each coat requires specific drying times, and the entire process can take several days or even weeks depending on weather conditions and the size of the house.
The final finish might involve techniques to create textures, adding to the complexity. In contrast, vinyl siding installation is generally quicker and less labor-intensive. The process involves attaching the siding panels to a framework, typically using nails or screws.
This is a relatively straightforward process that can be completed by a smaller crew in a fraction of the time it takes to apply stucco. The panels are typically interlocked, creating a seamless and weather-resistant barrier. Consider the example of a two-story house.
Stucco installation might involve scaffolding, multiple coats, and careful attention to detail to prevent cracking, whereas vinyl siding could be installed more rapidly using ladders and basic tools, with a noticeable difference in the overall project timeline.
Outcome Summary
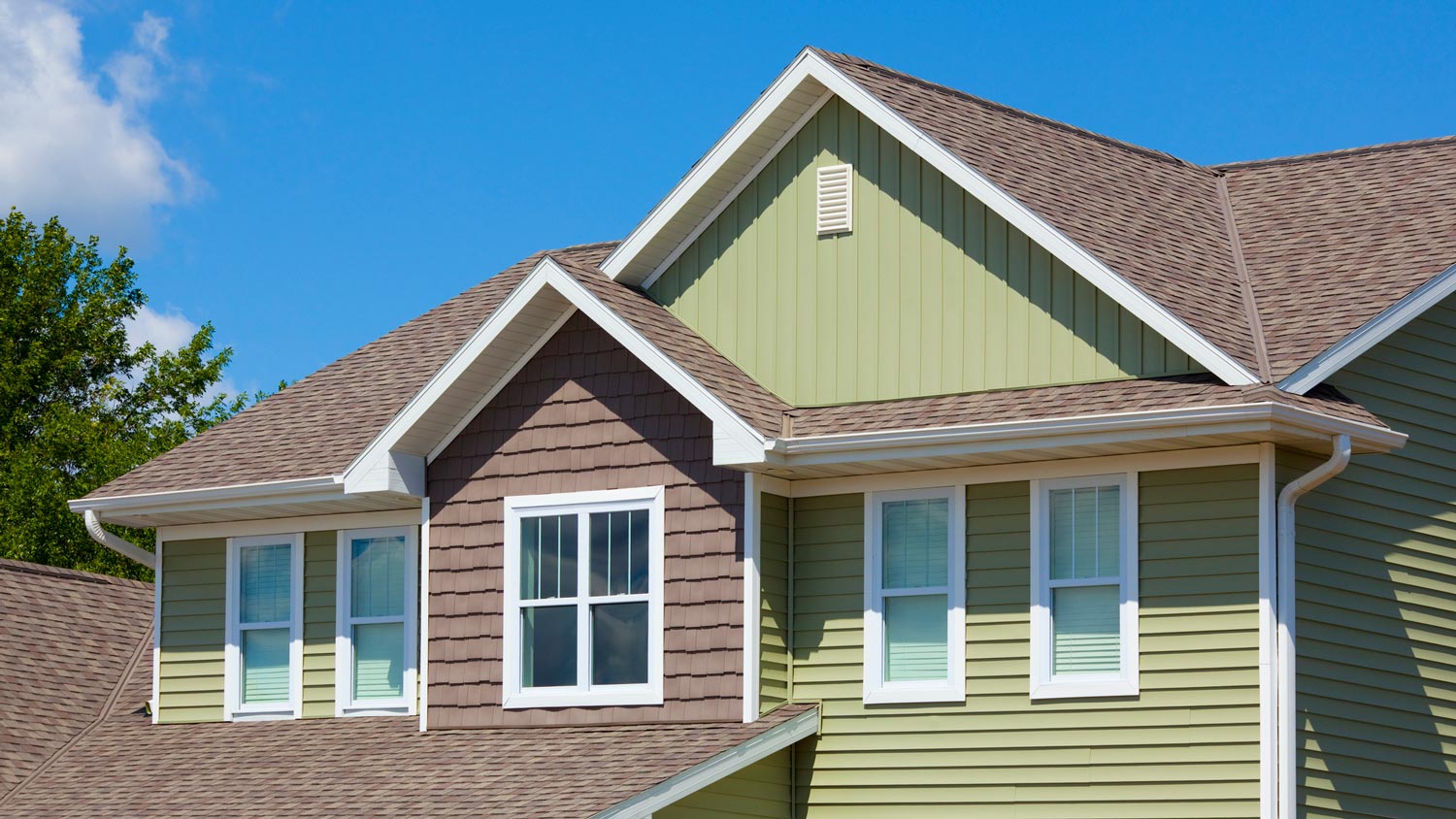
Ultimately, the cost to replace stucco with vinyl siding is a multifaceted calculation dependent on numerous variables. By carefully considering the detailed cost breakdowns presented here, along with the potential challenges and rewards, you can approach this home improvement project with confidence.
Remember to secure multiple quotes from reputable contractors, thoroughly research materials, and factor in potential delays to ensure a smooth and successful renovation.